5083 aluminum alloy sheet VS. 6061 aluminum metal sheets
Similarities Between 5083 and 6061 Aluminum
- High Aluminum Content: Both alloys share approximately 96% of their average alloy composition, making them predominantly aluminum.
- Versatility: They are both used in a variety of industries, including marine, automotive, and aerospace, due to their favorable strength-to-weight ratios and corrosion resistance.
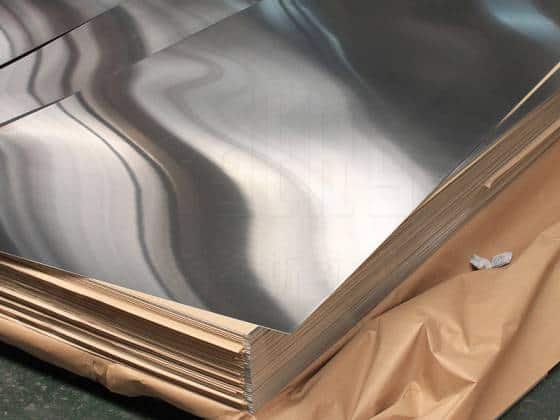
aluminum sheet interleaved with
paper
Key Differences Between 5083 and 6061 Aluminum
1. Strength and Heat Treatment
- 5083: This is a non-heat-treatable alloy that relies on work hardening to achieve its strength. It offers excellent performance in extreme environments, particularly at low temperatures.
- 6061: A heat-treatable alloy that can be strengthened through precipitation hardening. The T6 temper of 6061 provides higher strength compared to 5083, making it suitable for structural applications.
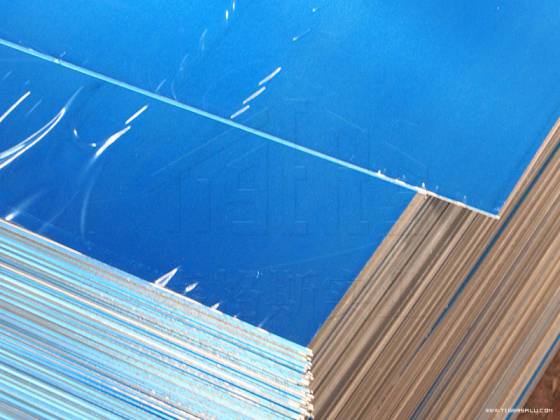
5083 H321 aluminum sheet with blue
films
2. Corrosion Resistance
- 5083: Known for its exceptional resistance to seawater and industrial chemicals, making it ideal for marine applications.
- 6061: Offers good corrosion resistance, especially when anodized, but is generally less resistant than 5083 in marine environments.
3. Weldability
- 5083: Exhibits excellent weldability with minimal loss in strength in the welded areas, which is crucial for shipbuilding and similar applications.
- 6061: While it can be welded, the strength in the heat-affected zones can be reduced, and post-weld heat treatment may be necessary to restore properties.
4. Machinability
- 5083: More challenging to machine due to its work-hardened state, which can lead to increased tool wear.
- 6061: Offers excellent machinability, especially in the T6 temper, making it a preferred choice for components requiring precise machining.
5. Applications
- 5083: Commonly used in marine environments, pressure vessels, and cryogenic applications due to its strength and corrosion resistance.
- 6061: Widely used in aerospace, automotive, and structural applications where higher strength and good machinability are required.
5083 aluminum alloy sheet application
- LNG ship construction
- Pressure vessels
- Storage tanks
- Welded structures (high strength)
- Armor plate
- Drilling rigs
6061 aluminum alloy sheet application
- Aircraft fittings, camera lens mounts, couplings, marines fittings and hardware, electrical fittings and connectors, decorative or misc.
- hardware, hinge pins, magneto parts, brake pistons, hydraulic pistons, appliance fittings, valves and valve parts.
Comparative Overview
Property | 5083 Aluminum | 6061 Aluminum |
Heat Treatable | No | Yes (e.g., T6, T651 tempers) |
Tensile Strength | Moderate | Higher (especially in T6 temper) |
Corrosion Resistance | Excellent (especially in seawater) | Good |
Weldability | Excellent | Good (may require post-weld treatment) |
Machinability | Fair | Excellent |
Typical Applications | Marine, cryogenics, pressure vessels | Aerospace, automotive, structural components |
Conclusion
Choosing between 5083 and 6061 aluminum alloys depends on the specific requirements of your application:
- Opt for 5083 when corrosion resistance, especially in marine environments, and excellent weldability are paramount.
- Choose 6061 when higher strength and superior machinability are needed, such as in aerospace or structural applications.
Understanding these differences ensures the selection of the appropriate alloy for your project’s needs.
Note: For detailed specifications and material properties, always refer to the manufacturer’s datasheets or consult with a materials engineer.
chemical composition
Grade | Max (%) | ||||||||||
Si | Fe | Cu | Mn | Mg | Cr | Zn | Ti | Others: Each |
Others: Total |
Al: Min. | |
5083 alloy | 0.40 | 0.40 | 0.10 | 0.4~1.0 | 4.0~4.9 | 0.05~0.25 | 0.25 | 0.15 | 0.05 | 0.15 | remainder |
More detail of 5083 aluminum
sheet/plate
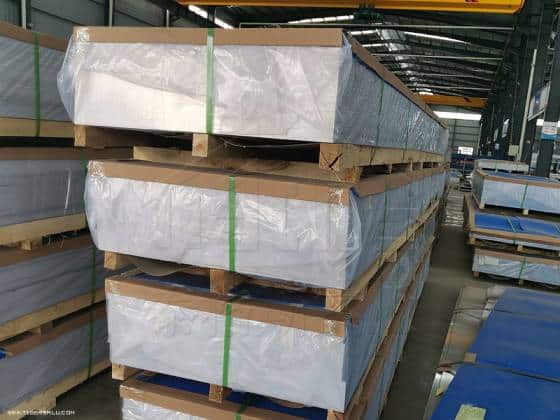
packages of aluminum sheet plate
Alloy | Si | Fe | Cu | Mn | Mg | Cr | Zn | Ti | Others: Each |
Others: Total |
Al: Min. |
6061 | 0.40~0.8 | 0.70 | 0.15~0.4 | 0.15 | 0.8~1.2 | 0.04~0.35 | 0.25 | 0.15 | 0.05 | 0.15 | remainder |
More detail of 6061
aluminum sheet and plate
Specification of 5083 aluminum sheet plate and 6061 aluminum plate
Dimension | Range |
Thickness | 0.5 ~ 6.0mm for sheet, max 500mm |
Width | 600 ~ 2,650mm |
- – Standard Width and Length: 4〃 x 8〃, 4“ x 4“ , 4 in. x 10 in. aluminum sheet, 5 x 10 aluminum
sheet, 48‘ x 96’ aluminum sheet, 1219 * 2438mm, 1220mm x 2440mm aluminum sheet, 1000mm x 2000mm aluminum sheet,
1250mm x 2500mm, 1219 x 2438mm, 1524 x 3048mm, 1500mm x 3000mm aluminum sheet. - – Surface Finish: Mill finish (unless otherwise specified), Color Coated, or Stucco Embossed
- – Surface Protection: Paper interleaved, PE/PVC filming (if specified)
- – Minimum Order Quantity: 3MT
In addition to the commonly used specifications, Tigers Aluminum can also produce 5052 ultra-wide and ultra-thick aluminum plates with internal stress relief and no deformation during cutting, and the width is 2650mm, the thickness is 500mm.
The difference between 6061 alloy and other alloys
different with 5052 alloy aluminum
5052 aluminum and 6061 has magnesium as a primary alloying element. In the case of 5052, it is the only primary alloying element. 6061 has silicon as well. One of the key benefits of this alloy is its high level of weldability compared to other alloys . For projects where the weldability is key, it is worth considering.
One downside to 5052, though, is that it is not heat treatable. It is good for a variety of welding applications and it works well in marine applications due to its high corrosion resistance.
Description of 5083 and 6061 on wikipedia:
The above content is the difference between 5083 aluminum alloy and 6061 aluminum alloy.
Most of aluminum 5083 sheet/plate and 6061 aluminum plate stock is available in full size and custom cut lengths.